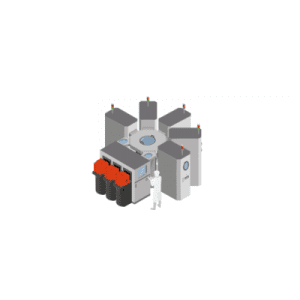
With the introduction of larger and heavier 300 mm wafers, semiconductor factories required a significant change in the automation of production lines. They became more automated to increase throughput, to automate material delivery to each equipment by using robots (Automated Guided Vehicles or AGVs), to refine process controls and to get accurate analysis to track equipment performances. Several standards were specified, known as GEM300 (or SEMI300) because their creation and adoption coincided with the first 300 mm wafer factories. However, there are no features in these standards specific to the wafer size. The new features that GEM300 has introduced in the semiconductor industry were so essential that they were adopted by all the semiconductor industry worldwide within a few years
What is the role of GEM300?
SECS/GEM were the initial standards for configuring and controlling the communication flows between the factory and the equipment. GEM300 completes these to empower equipment autonomy on material entrance with automated carrier delivery and removal, validation of material identification ensuring that the correct material has been delivered to the machine. Afterwards, factories specify the process job to be performed on the equipment and follow process steps. Last but not least, substrates are tracked inside the equipment, and the efficiency of the equipment is measured and analyzed.
Worldwide, more and more semiconductor factories require equipment suppliers to fulfill GEM300 standards to interact with factory automation including for smaller wafer sizes such 150mm or 200mm.
GEM300 challenges
The main challenges for equipment suppliers are first to understand which GEM300 functionalities are applicable on their equipment, secondly, to ensure that their implementation of GEM300 is compliant with the SEMI standards, and finally to communicate with the Manufacturing Execution System (MES or Host) during deployment and tool acceptances in fabs (Fabrication Areas). Of course, all of that must be integrated in a short delay to ensure the process or inspection tool is in the right time to market.
GEM300 functions
Five major functions are the basis of GEM300 as described below:
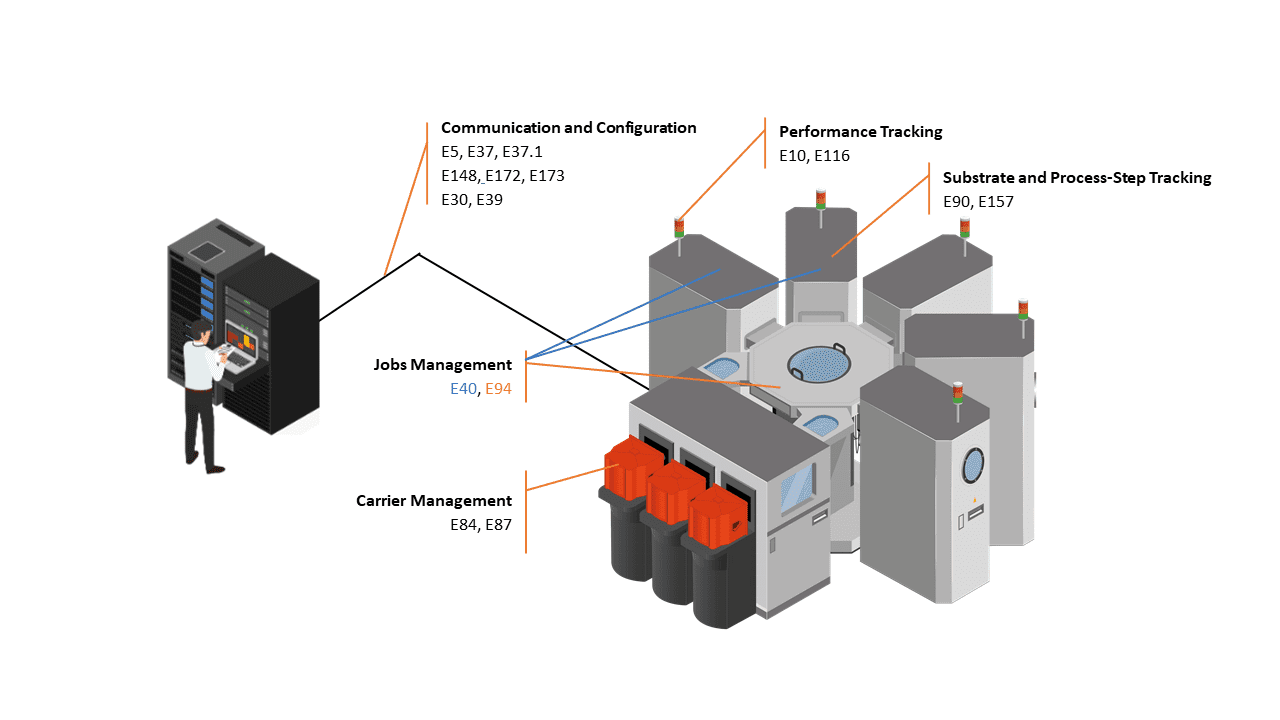
- Communication and Configuration: GEM (SEMI E30) is the core component and associated to SEMI E5, E37 and E37.1, it allows to establish and configure the communication between the equipment and the factory. All fundamental capabilities of GEM are used for data collection, alarm management, equipment configuration, recipe upload/download, equipment terminal services, clock, and control definition (local/remote). A more details SECS/GEM introduction is available here.
- Carrier Management: SEMI E84 and E87 manages the delivery, the handling and the validation of the material. The objective is to validate that the expected material has been delivered to the equipment.
- SEMI E84 deals with the handoff of carriers by an Automated Material Handling System (AMHS) or Overhead Hoist Transfer (OHT).
Thanks to SEMI E87, substrates can be accessed for processing after validations. The equipment itself can validate the ID and Slot map following a Bind service (Equipment Based Verification) or by the host with a ProceedWithCarrier service (Host Based Verification). - Jobs Management: SEMI E40 and E94 specify jobs performed on the equipment, describing the substrates to be processed and the recipes to be used.
SEMI E40 defines Process Jobs that contains a list of materials and the name of recipes for the process. In addition, it allows the adjustment of the parameters to be used during the process.
SEMI E94 defines Control Jobs that manages a set of Process Jobs. - Substrate and Process-Step Tracking: SEMI E90 tracks all substrate movement inside the equipment, and SEMI E157 the performance of process steps.
The substrate ID can be verified if the equipment contains a reader. - Performance Tracking: SEMI E10, E116 measure and analyze the performance of equipment. This function becomes more critical for semiconductor factories for preventive and predictive maintenance to reduce downtimes and anticipate some root causes of alarms.
The complete standard list is provided hereafter:
SEMI Standard | Title |
Communication and Configuration | |
E30 | Generic Equipment Model for communications and control of manufacturing equipment (GEM) |
E5 | Specification for Semi Equipment Communications Standard 2 message content (SECS-II) |
E37 | High-Speed SECS Message Services (HSMS) Generic Services |
E37.1 | High-Speed SECS Message Service Single Selected Session Mode (HSMS-SS or HSMS-SSS) |
E39 | Object Services Standard: concepts, behaviour, and services |
E148 | Specification for Time Synchronization and Definition of the TS-Clock Object |
E172 | Specification for SECS Equipment Data Dictionary (SEDD) |
E173 | Specification for XML SECS-II Message Notation (SMN) |
Carrier Management | |
E84 | Specification for enhanced carrier handoff parallel I/O interface |
E87 | Specification for Carrier Management (CMS) |
Jobs Management | |
E40 | Standard for Processing Management |
E94 | Specification for Control Job Management |
Substrate and Process-Step Tracking | |
E90 | Specification for Substrate Tracking |
E157 | Specification for Module Process Tracking |
Performance Tracking | |
E10 | Specification for Definition and Measurement of Equipment Reliability, Availability, and Maintainability (RAM) and Utilization |
E116 | Specification for Equipment Performance Tracking |
GEM300 and Agileo Automation
Agileo Automation has a team of experts with a huge experience in SECS/GEM connectivity. Our teams have developed control and connectivity software for 30+ different semi-conductor and PV tool models deployed in 50+ fabs in 15 different countries. We provide libraries, services, and supports to efficiently integrate your SECS/GEM and GEM300 interface in the factory automation.
For GEM300, we developed Agil'GEM300, a complete .NET/C# solution for the connectivity. It handles the complexity of GEM300 automation and provides a simple interface to connect to the devices, user interface and the factory host.
Meanwhile, the communication interface with the MES was standardized (software automation), automation hardware for carrier loading, wafer loading into process chambers or inspection chambers was also standardized by a few vendors (hardware automation) hence allowing the creation of an equipment automation software framework.
GEM300 with the A²ECF framework
Agileo Automation Equipment Controller Framework (A²ECF Semi) dramatically reduces the development effort for a GEM300-compliant equipment software, accelerating the time-to-market of this equipment. With its support of either GEM or GEM300 together with its drivers for major robotics loaders and FOUP openers, OEMs can focus on their core business and deliver tools on time with built-in connectivity.
Do not hesitate to get in touch with us to help you to:
- Answer GEM300 questions in Request For Quotation (RFQ) from you customer,
- Specify the SECS/GEM interface for your equipment,
- Integrate this specification on your equipment or support your teams to integrate libraries,
- Validate the GEM300 scenario applicable on your equipment using Speech Scenario, a powerful test scenario application to validate real world production uses case,
- Support you at your customer site for tool acceptances.